Guyson robotic shot peening machine for aerospace parts
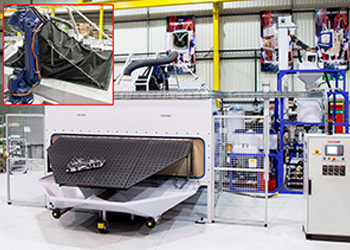
Leading industrial finishing equipment manufacturer Guyson International has designed and built a robotically controlled shot peening system for batch peening multiple aerospace parts to AMS2432 computer controlled shot peening standards.
Photo caption: Guyson Robotic Shot Peener with multiple Almen test strip sample on blast table and inset photo of robot at the back of the machine
Controlled shot peening is regularly being specified by the aerospace, automotive and nuclear industries to enhance component service life. It is a cold working process in which the surface of the component being processed is bombarded with small spherical media. Each piece of shot striking the surface of the component acts as a miniature peening hammer, deforming the component surface and causing a small indentation or dimple. The overlapping dimples develop a thin layer of metal in residual compressive stress at or near the surface. Since nearly all fatigue and stress corrosion failures start at the surface of a part, the compressive stresses induced by shot peening can considerably increase component service life.
The Guyson shot peening cabinet itself is 3 metres wide by 1.8 metres deep and features a rotary indexing turntable which allows the parts to be loaded and off loaded external to the blast chamber and so can be performed whilst the robotic shot peening occurs inside the cabinet, reducing the total cycle time. To ensure no blast media escapes during the peening process the turntable is sealed around the perimeter with an automated inflatable seal. This deflates prior to the turntable rotating and then re-inflates prior to blasting. A subsequent benefit of this Guyson sealing technique is the reduced airborne noise compared to that associated with traditional conveyor type machines required for large flat or ribbed work pieces. The 180° indexing turntable is also designed with light guarded safety features that ensure no person can be within the load area perimeter whilst the turntable is indexing.
Below is a link to a video that includes the Guyson robotic shot peening machine in action.
Robotically Controlled Shot Peener Video
The four peening nozzles are precisely manipulated by the robot arm to maintain the optimum surface speed, blasting angle and exact stand-off distance from the components at all times. With clever programming the Guyson system can replicate an eight nozzle head to maintain optimum peening angles for complex geometry work pieces verified by Almen fixtures replicating critical features. The ABB robot arm itself has a 2.55 metre reach and a 40 kg load capacity and is located within a safety enclosure to the rear of the cabinet. Access for maintenance purposes is only allowed by ‘fortress’ type interlocks. This is where the one key has to be taken out of the control system so disabling it and then used to open any subsequent access doors; so preventing any possibility of the robot arm moving when operators are in close proximity.
Firstly the aerospace parts are strategically positioned across the surface of the angled peg board designed blast table. This provides maximum flexibility of component mix and a high degree of throughput. Components are located on the polyurethane coated table bed with pegs which secure them in place whilst the table rotates and shot peening is undertaken. The operator then presses the two handed start function and the table rotates through 180°, once in the correct position, the rubber collar inflates, sealing off the blast chamber and shot peening can commence. Further parts loading or unloading now takes place.
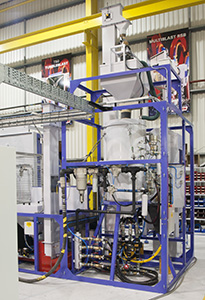
The shot peening media delivery is via a twin chamber pressure pot, providing continuous flow during the long peening operations. The pot is fitted with high and low level sensors on both chambers allowing for a controlled media feed between chambers without interrupting shot flow. Media is fed from the valve, one for each nozzle, at the base of the pressure pot into the cabinet via heavy duty hose connected to the four blast nozzles. Critical media flow rate is controlled by automated grit valves passing media through a MagnaValve, one for each nozzle, with monitoring that relays information of media flow to a controller to ensure consistent flow.
After peening the spent media falls to the bottom of the blast cabinet and travels out of the base of the cabinet hopper via Archimedes type auger screw to a bucket elevator to be fed into the reclamation system for grading and reuse. A bucket elevator is used due to the heavy weight of the media. A three deck sieve separator removes any oversized particulates via the upper decks to a waste bin. Shot that is within size tolerance is returned to the storage hopper, located above the pressure pot, via the lower sieve deck. Particulates smaller than tolerance levels pass through all the decks, also into the waste bin.
Also incorporated into maintaining accurate media size and shape is a roundness classifier which samples 10% of the shot media on each pass during the process and removes any miss-shaped shot. The Guyson sieve and roundness classifier maintain the shot to AMS2431 size and shape control specifications.
A large GC30-K7 dust collector unit removes the dust laden air from the shot peening cabinet and provides continuous cleaning of the six filter elements during the operation of the blast machine. A secondary HEPA filter is also specified for further reductions in contamination and Magnahelic differential pressure gauges are fitted to the dust collector to monitor the condition of the filter cartridges and indicate when intervention is required.
The entire shot peening process is controlled by a graphical HMI unit operating a PLC with system parameters being monitored though a series of graphical representations allowing an easy understanding of what is happening throughout the system and enabling full operation and control from one point.
Customers of manual or automated blast systems are encouraged to submit sample components for free feasibility testing to the company’s extensive development workshop at Skipton, England and initial enquiries for similar shot peening systems are invited now.