Guyson robot loaded shot peening automation with traceability
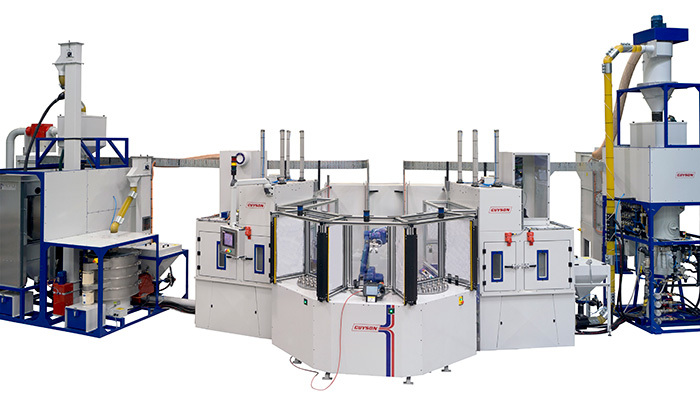
Guyson International, the UK’s foremost industrial finishing equipment manufacturer, has designed, manufactured and installed into an international manufacturing company, a large automated, robot loaded, dual media shot peening system for fatigue life enhancement, typically required in aerospace and medical applications.
The system comprises two Guyson Multiblast® RXS900 automated blast systems; one for steel shot peening and one for glass bead peening, with robotic work piece transfer between the two blast systems. The computer controlled process was designed to meet AMS2432 standards demanded by the client. This fully integrated process with traceable record keeping delivered increased capacity with less labour compared to the existing process.
Batches of 12 workpieces in a dual indexing carousel for In/Out control are picked up one at a time by an ABB robot and sequenced through the system. Suitable for turbomachinery turbine blades or medical implants, each piece is loaded into the six rotary indexing stations of the Guyson RXS900 (Rotating indeXing Spindle) shot peening system located to its left. The components index clockwise through two shot peening stations - both equipped with two boron carbide blast nozzles, four in total, which vertically stroke up and down the workpiece, delivering the correct Almen intensity, at the correct impingement angle and providing 100% surface coverage.
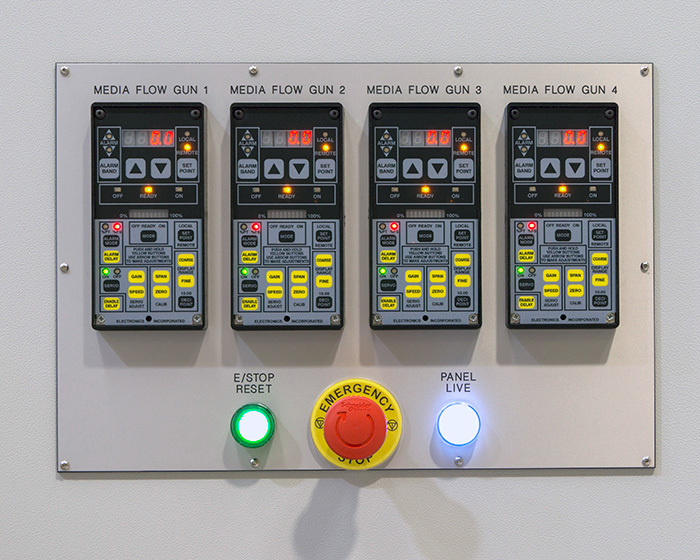
Steel shot blast media is delivered to the blast nozzles via a 300 litre twin chamber pressure pot, allowing for continuous media flow during the long peening operation. To meet AMS2432 standards media flow rate is monitored and controlled with Magnavalves whilst closed loop peening air pressure, spindle RPM and vertical gun traverse rates are all held within tight specifications. An airwash station, separated by an internal pneumatic vertical door, removes residual dust and blast media from the components prior to removal from the blast machine.
Due to the heavy weight of steel shot used in the peening process, a bucket elevator transfers the used blast media, via Archimedes type auger screw, into the reclamation unit to maintain blast media quality. This unit comprises a 30" 3-deck sieve separator which removes any oversize particulates via the upper decks to a waste bin. Shot that is within size tolerance of the process is returned to the storage hopper via the lower deck. Any particulates deemed smaller than tolerance pass through the decks to a waste bin. An integrated spiral roundness classifier removes up to 10% of the blast media during the reclamation process and removes any mis-shapen shot, before returning good media to the system.
A large reverse jet pulse cleaning dust collection unit provides automated cleaning of the four filter elements during the operation of the blast system, this being particularly beneficial for continuous blast operations. The dust collector is fitted with secondary HEPA14 filter, back-flap valve and explosion relief valve.
Following steel shot peening a de-contamination glass bead peening operation is undertaken. The same ABB robot unloads each station as it exits and transfers components to the glass bead peening system; where bead peening takes place in a similar blast system, but using glass bead.
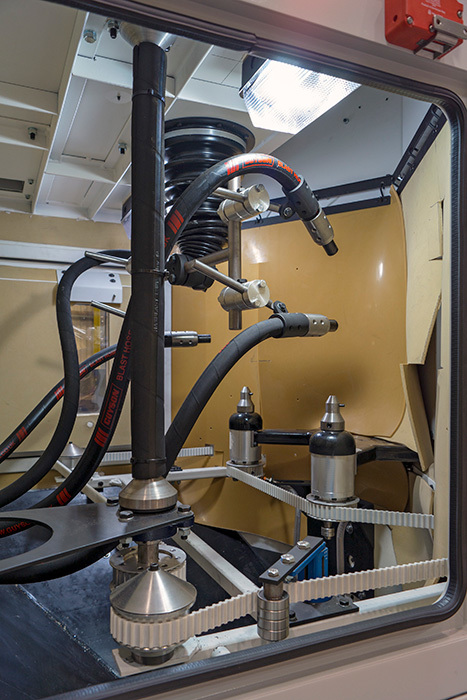
The RXS900 glass bead peening system differs from the shot peening system by having a Guyson built cyclone reclamator. This extracts everything from the base of the blast cabinet and separates out re-usable blast media from the dust and debris created by the blast process. The lighter particulates being drawn off into the dust collection unit, the heavier blast media flows down the cyclone body and into the media reservoir position above the pressure pot ready for re-use.
On exiting the glass bead peening system the robot transfers the processed components to the right hand unloading carousel, ready for the operator to remove. The operator is not able to access the blast area as both it and the robot are encased in a safety enclosure fitted with fortress interlocks. Once both systems are fully loaded, a continuous production run of one part in and one part out follows.
At the completion of the batch set the un-load carousel indexes, presenting the work pieces to the operator. Simultaneously for traceability, batch processing records are written to an SD card or network computer to document and record the status of each piece within the batch.
Prospective user of Guyson automated blast systems are encouraged to submit sample components for free feasibility testing to the company’s extensive development test centre located in Skipton, England. Please contact Guyson’s customer service department now to arrange free blast trials on your components, prove the process and make recommendations on the most suitable blast system for you – call +44 (0)1756 799911 or email info@guyson.co.uk