Guyson robot blasting prior to thermal spray coating
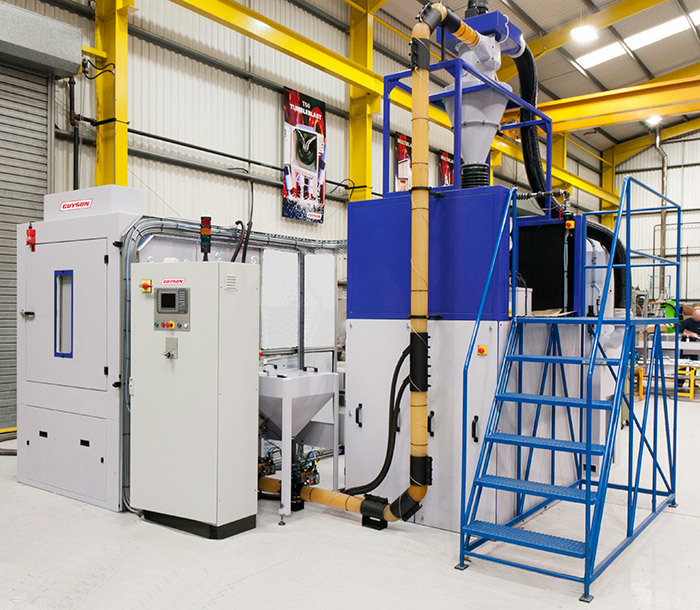
Finishing equipment manufacturer Guyson International has designed, built and installed a twin pressure pot, Guyson RB10 PF robotically controlled blasting system into a world leading manufacturer of high-performance coatings, for the dual application of keying the surface of aerospace seal rings prior to plasma spraying and the surface preparation of turbine blade tips prior to thermal spray coating.
The Guyson RB10 blast cabinet has internal dimensions: 1500 mm (w) x 1500 mm (d) and is fitted with large doors, with viewing windows, on two sides of the cabinet allowing access for loading and unloading and maintenance purposes. Fortress type interlocks prevent robot movement, blasting or spindle rotation when a door is open. The blast cabinet is fully lined with energy absorbing hanging rubber sheet for sound absorption and resistance to wear and additional sacrificial hanging rubber sheets are provided in the line of overspray.
A 5 mm boron carbide blast nozzle is robotically manipulated at the fixtured component. The robotic manipulation of the blast nozzle maintains the optimum surface speed, blasting angle and the exact offset distance from blast nozzle to component – be that either the aerospace seal rings or the turbine blade tips. The robot positioning the blast nozzle, is an ABB foundry plus robot system, located to the rear of the cabinet and encased within a safety enclosure fitted the with fortress type interlocks providing access for maintenance or adjustment purposes, yet ensuring no one can enter the space whilst operating. A small 7th axis turntable is fitted in the middle of the blast chamber and is designed to accommodate the customers varied fixtures, due to the multiple uses of the cabinet. The robot fixture holds two blast nozzles – each with a separate blast media supply. But only the one appropriate nozzle linked to each of the applications is active at any one time.
Blasting is achieved via either of the two Guyson Model G55 pressure pots (55 litres each), these are used to generate the blast stream within the blast chamber, with media being fed from the appropriate pressure vessel into the cabinet through heavy duty hose to the blast nozzle. The flow of media is controlled by a manual pinch valve mounted on the cone of the pressure pot which regulates the volume of media being released into the compressed air stream.
High/low media level sensors are fitted to monitor the level of blast media within the G55 pressure pot and will display a signal on the control panel if media level is at a high or low level and there are additional media level sensors for overfill to each pressure pot. A media pressure pot reservoir positioned over each pressure pot, complete with control valves, regulates the volume of media being released to the blast system.
The blast media quality is maintained, to give a more consistent surface finish, via a GuysonCY600/12 Cyclone Reclamator mounted above a sieving system and the twin pressure pots. The cyclone extracts everything from the bottom of the blast cabinet and separates out good reusable blast media from the dust debris. The good blast media is then passed through the 24" four-deck sieve. This is designed to take out re-usable blast media from the dust and blast debris, allowing only good media of the correct size to return to the media delivery system, it does this by passing all the extracted media and waste through a series of sieves which separate it out appropriately and then deposit the remains in the correct bins. The sieve, cyclone and pressure vessels are contained inside a tower framework, with cladding panels to reduce noise and a maintenance access ladder on the framework to allow for inspection and maintenance of the sieve system.
A highly efficient model C800 Cartridge Dust Collection unit is fitted to draw off the dust laden air from the cyclone reclamator, passing it through the twin pleated micronic polyester filter cartridges which are periodically cleaned via an auto air pulse alternating between the cartridges. A magnahelic differential pressure gauge is used to monitor the condition of the dust collection filter cartridges and indicate when the cartridges require replacing. The dust collector is also fitted with a HEPA secondary filter to protect the system should the primary filter cartridges fail and acts as a safety feature to protect the local area in the event of a leakage on the primary filter. Additionally the dust collector is fitted with an explosion relief panel that is joined to a vertical ducting assembly, to takes the force upwards should the explosion relief panel be triggered, a two metre exclusion zone is required above the top of the ducting.
Monitoring and control of the complex blast system is provided via a Mitsubishi PLC/HMI graphical display which gives a real time visual display of what is happening throughout the system. Downtime is reduced as fault notification can be programmed to display specific screen messages regarding warnings and failures. Also parameter changes can be easily effected making future proofing more feasible and such simpler. A three colour beacon allowing awareness of certain events during the machine processes e.g. fault alarm or machine ready.
Guyson are inviting prospective robotic blast customers to get in touch for initial talks and demonstrations of the technology involved, including free component blast trials, especially from those involved in the aerospace, medical, thermal spray and oil and gas sectors with components such as turbine blades, medical implants, industrial pumps, turbo chargers and aerospace MRO components.
About Guyson
Guyson International Limited is a privately owned family company with a world-wide reputation for excellence in the design and manufacture of blast finishing, spray wash and ultrasonic cleaning equipment. Formed almost eighty years ago, the company is registered to BS EN ISO 9001: 2008 and BS OHSAS 18001:2007, and its head office is located at Skipton, North Yorkshire, in the north of England. Guyson has four international subsidiary companies: Guyson Corporation of the USA, located in Saratoga Springs, New York State; Guyson SA, situated near Paris, France; Guyson Sdn Bhd in Penang, Malaysia; and Guyson CN, in Wuxi, Jiangsu Province, China.
Contact
Finishing Equipment - Sales, Technical, Demonstration & Manufacturing