Guyson automated blast system removes heat treatment salts from HSS End Mills
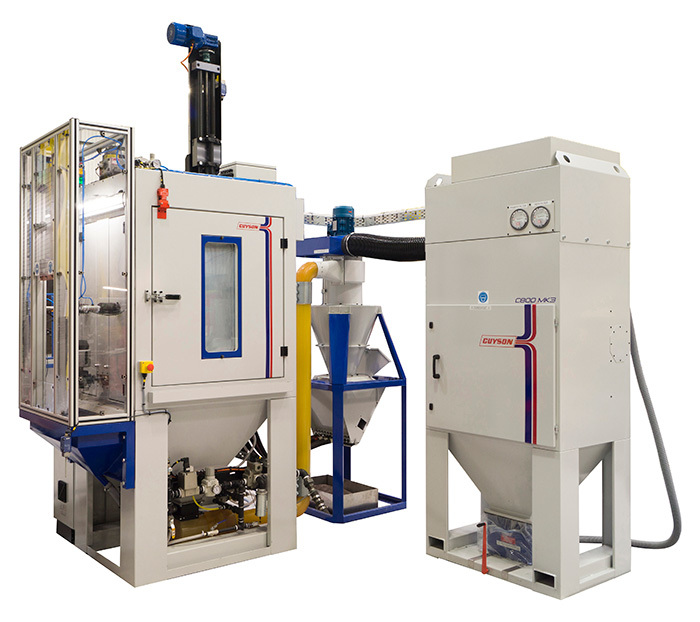
A leading overseas manufacturer of high quality tooling has recently installed an automated Guyson Multiblast® RXS400 blast system for the dual purposes of removing of oxidation and heat treatment salts from HSS Round End Mills and to provide an attractive cosmetic surface finish prior to applying anti-rusting oil. Along with the surface preparation of tooling, typically these highly compact automated blast systems are often specified, by customers, for grit blasting turbine blades and medical implants.
Photo caption: Guyson Multiblast RXS400 with Cyclone and Dust Collector
Blast trials were initially undertaken, at Guyson’s Component Finishing Centre in Skipton, to prove the process, establish process timings and optimise the most suitable blast media. The compact and automated Guyson RXS400 (Rotating indeXing Spindle) system was selected as the most appropriate machine to suit the customers budget and production output targets. The process now achieves a consistent white metal finish in the required time, with virtually no operator involvement apart from load and unloading; thus removing the vagaries of manual blasting and leaving the operator to perform other duties if required.
The Guyson Multiblast RXS400 machine is a twin spindle rotating indexing blast system which provides two driven work spindles at opposite ends of a rotary arm. This arrangement allows one of the spindles to be outside the blast chamber during the blasting operation for simultaneous loading or unloading of the component, whilst the other is inside the blast cabinet being active.
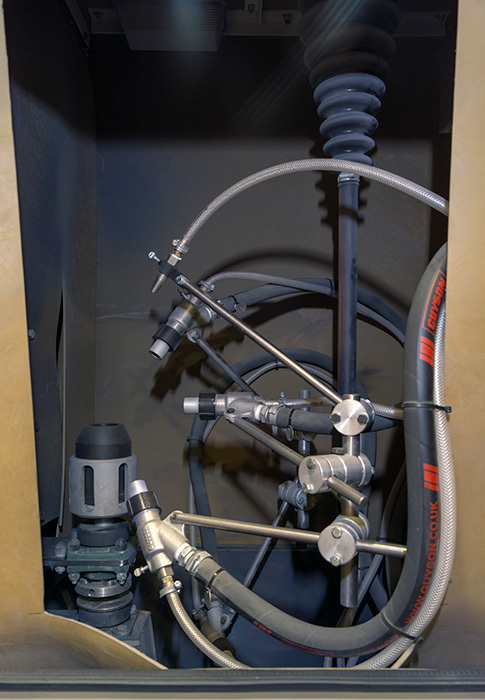
Surface blasting of the HSS drill components is achieved with three powerful Guyson model 900 blast guns mounted on a vertically traversing arm, stroking up and down the various drill lengths, and then a post blast compressed air wash is directed at the drills to remove residual dust and blast media.
The external area around the loading zone is enclosed with an aluminium frame fitted with clear Perspex panels and a vertically sliding pneumatic safety door fitted to the middle of the front panel. This vestibule helps minimise any sound escaping from the blast zone. Hinged pneumatic entry and exit doors allow the component in and out of the blast zone. On the right hand side of the cabinet is a full width side opening door to facilitate easy access for maintenance and setting up purposes. For safety reasons this door is interlocked to prevent blasting when open.
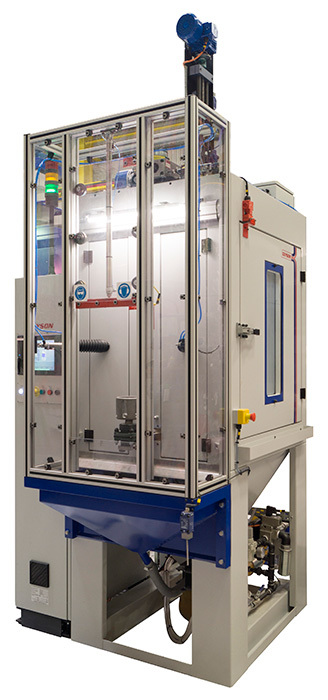
After grit blasting, the used blast media is extracted via a Guyson CY600/12 cyclone reclamator that separates out the re-usable blast media from dust, blast debris and undersized media. The extraction system is completed with a Guyson model C800 twin cartridge dust collector fitted with a secondary HEPA 14 filter. The entire blast system is controlled via a Mitsubishi PLC/‘Graphic Operator Terminal’ (GOT), with full colour display screen, which facilitates repeatable blast settings to be simply stored and retrieved in quick access menu systems.
Prospective user of Guyson blast or wash systems are encouraged to submit sample components for free feasibility testing to the company’s extensive ‘Component Finishing Centre’ at Skipton, England.
About Guyson
Guyson International Limited is a privately owned family company with a world-wide reputation for excellence in the design and manufacture of blast finishing, spray wash and ultrasonic cleaning equipment. Formed eighty years ago, the company is registered to BS EN ISO 9001: 2015 and BS OHSAS 18001:2007, and its head office is located at Skipton, North Yorkshire, in the north of England. Guyson has four international subsidiary companies: Guyson Corporation of the USA, located in Saratoga Springs, New York State; Guyson SA, situated near Paris, France; Guyson Sdn Bhd in Penang, Malaysia; and Guyson CN, in Wuxi, Jiangsu Province, China.
Contact
Finishing Equipment - Sales, Technical, Demonstration & Manufacturing