Springs and Wire Forms
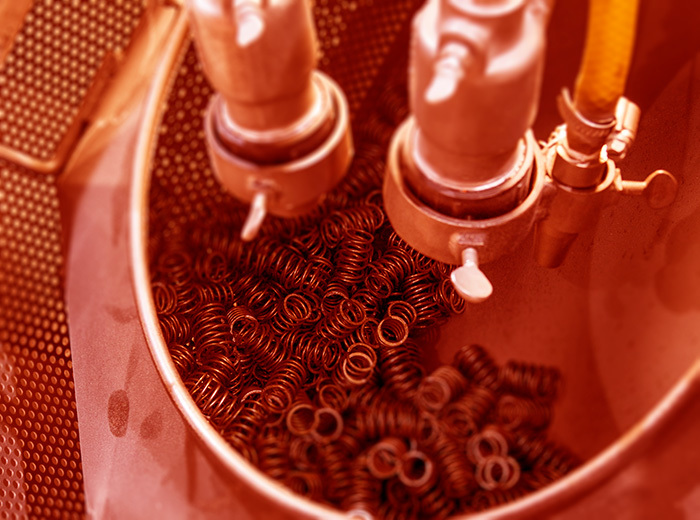
If your spring or wire form components need deburring, descaling, degreasing, cosmetic finishing or lightly etching, prior to a coating, plating or painting process or shot peening for added strength and to increase component fatigue life, then contact Guyson now to learn how we may be able to save you time and money.
Guyson manufactures a selection of batch-orientated blast finishing and cleaning equipmentspecifically designed for efficiently handling such workloads and if in the near future you are intending on replacing or installing any blast or cleaning equipment for this type of work I’m sure it would benefit you to take a look at our range.
One such spring company installed a ‘Kerry’ branded Microsolve 350 Co-Solvent cleaning system, along with a Guyson Multiblast® T50 Tumblebasket system. Both Guyson machines were installed to perform a dual function of providing higher levels of automation, whilst also improving product quality, during the production of compression springs. The Microsolve 350 solvent cleaner was used to remove mineral drawing oil from the formed springs before heat treatment, and then subsequent descaling in the T50 Tumbleblaster to deliver an improved surface finish.
Degreasing the springs
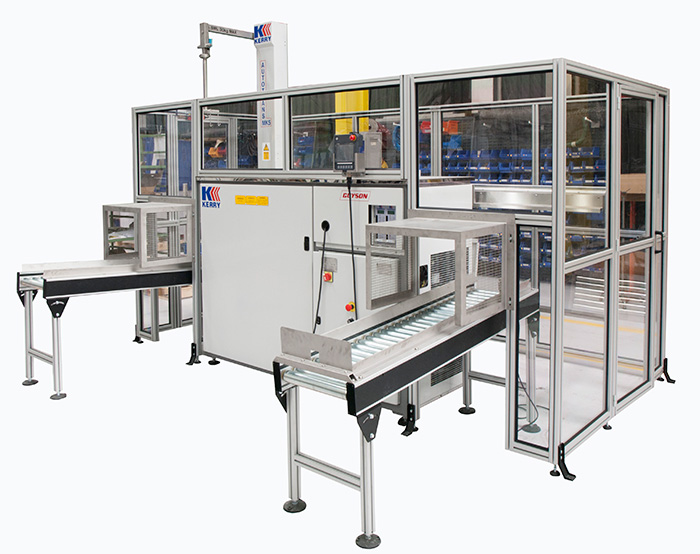
Guyson’s ‘Kerry’ Microsolve 350 Co-Solvent cleaning system provides two ultrasonic cleaning stages, both with filtration, followed by vapour rinsing and freeboard drying.
In the first cleaning tank, a mixture of HFE (hydrofluoroether) and a hydrocarbon solvating agent removes the mineral oil from the compression springs. Large quantities of dirt and oils can be taken up by the solvating agent, and this makes the process particularly suitable for heavy-duty cleaning.
In stage two, pure HFE distillate removes any residues left on the springs carried over from the primary cleaning tank. Both heated cleaning tanks include base mounted ultrasonic transducers powered by a Guyson ultrasonic generator, this combination delivers both a very robust cleaning activity with flexible power delivery. Cleaning is followed by rinsing in the vapour zone, above the tanks, and then a dwell in the freeboard zone to dry the springs.
Finishing the springs
After processing the springs in the Microsolve 350 the springs are now clean of mineral drawing oil, so when they go through the subsequent heat treatment process there is less underlying scale on them than was previously the case. Now batch descaling in the Guyson T50 tumbleblaster is undertaken in a shorter time and with less scale, which results in a better finish, reduced production time and reduced blast media usage.
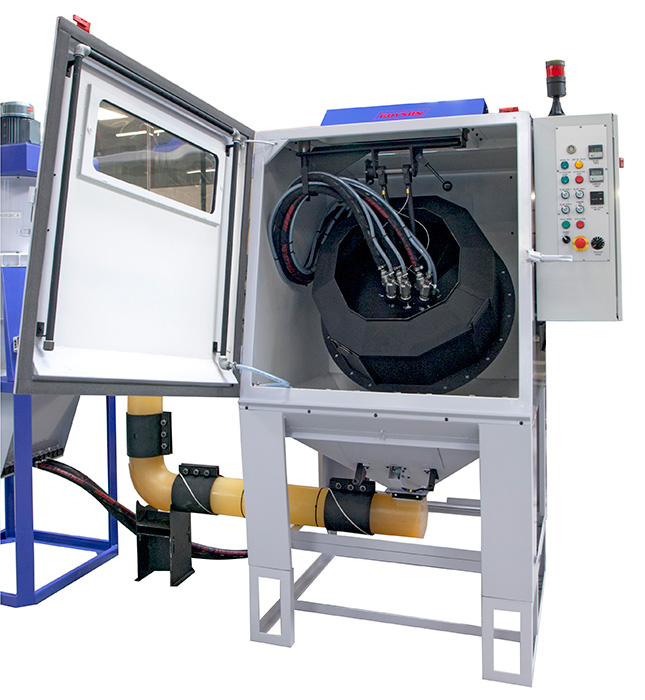
The installed Guyson Multiblast T50 tumbleblast machine has been modified from the standard version to increase the height of the cabinet, allowing a delivery shute mechanism to be installed underneath. When the machine has finished descaling a whole batch of springs they can be offloaded directly out of the internal basket into a container underneath the machine via a shute that is clipped in place for the purpose, thus reducing manual handling.
The T50 Tumbleblaster has a maximum load capacity of 50 kg’s and each batch is blasted by a cluster of three Guyson Model 900 blast guns fitted to fully adjustable arms, allowing optimum blast coverage and a speedy batch time. Airwash is also provided so the springs can be removed from the basket totally free of blast media.
For smaller volumes, and in a smaller footprint, Guyson also offers the T40 Tumblebasket with a maximum load capacity of 35 kg.
Spring or wire form manufacturers are encouraged to contact Guyson for free trials on their products and to see how they too could benefit from using Guyson finishing technology.