Aerospace
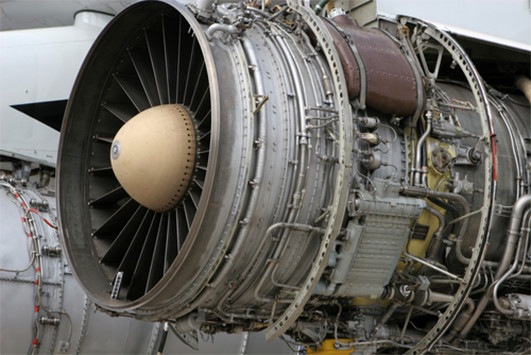
Guyson is a genuine worldwide player in the aerospace market providing a wide range of industrial finishing products for both original equipment manufacture (OEM) and maintenance, repair and overhaul (MRO) work.
Blast Finishing
We have a wide range of standard blast cabinets as well as automated blast systems, including robotically controlled, in both suction (SF) and pressure feed (PF) versions. The premier quality Euroblast manual cabinet range is available in seven standard sizes and has a vast array of ‘options’ available which can be tailored to specific applications, such as maintenance, repair and overhaul (MRO) of landing gear in an extra-large two-metre cabinet, with additional armholes, for instance.
Typical manual blast aerospace applications include: the removal of carbon deposits from turbine blades using natural sources with a non-aggressive blast media such as corn cob. Or at the other end of the scale, very aggressive blasting for casting investment removal with one of our PF blast systems, using hard angular abrasive blast media. Paint stripping with plastic blast media, especially as part of aerospace MRO is also very common usage in our larger cabinets, as is removing step lines from rapid prototypes in our smaller ones also the removal of dust and fluff with air only blow off. Small micro blast units, incorporating a pencil-like blast nozzle, are also available for intricate blasting of turbine blade cooling holes.
The Guyson Tumbleblast T40 and T50 provide speedy and effective blast finishing for batch processing (cleaning, deburring, deflashing, cosmetic finishing and surface preparation) of smaller components such as aerospace fasteners which can be used in engines, wings, fuselages and landing gear. These tumble blast machines provide fast cycle times, repeatable process quality and ease of operation.
Guyson can provide a multitude of automated grit blasting options including multiple gun and robotically controlled. Multiblast® automated blast systems with multiple guns are engineered to ensure a high level of process and machine control. This ensures an accurate, consistent and uniform finish to every part. These systems are used for a wide range of aerospace applications, including surface conditioning of turbine blades prior to thermal spraying, glass bead peening for refurbishing turbine compressor blades and peening of precision gears.
Guyson also has several options of robotically controlled blast machine with either the component or the gun being manipulated by the robot and many of these have been used for shot peeningturbine blades and aerospace structures.
Ultrasonic Cleaning
Guyson's 'Kerry' branded ultrasonic cleaning products include the KS ultrasonic tank range with a variety of tank sizes, holding from 21 to 275 litres, for robust quality cleaning in applications such as aerospace MRO. Spray rinse options are available with the Kerry UCR (ultrasonic, clean, rinse) product line. Kerry KST submersible transducers are designed for applications such as retrofitting to existing cleaning tanks or incorporation into new machines on an OEM basis. The CRD 450 (clean, rinse, dry) is a three-stage aqueous cleaning system suitable for applications such as low volume PCB defluxing, metal finishing, 'Tam' panel cleaning and maintenance cleaning.
For high-quality precision cleaning Guyson offers the aerospace market the Microclean (aqueous) and Microsolve (solvent) cleaning systems which operate most efficiently when fitted with Guyson Autotrans lifting automation, to provide fully automatic operation.
The standard Microclean four-stage aqueous cleaning system (heated ultrasonic clean, rinse, rinse, warm air dry) is suitable for a wide range of aero engineering and aero electronics cleaning applications. Succesful Microclean applications include removing polishing compounds from optical glass and plastic lenses, cleaning valve components, removing swarf and machining oil from hydraulic components and cleaning, rinsing and drying turbine blades prior to NDT penetrant testing.
Alternatively, the Microsolve Mono and Co-Solvent ultrasonic cleaning systems use HFE (hydrofluoroether) or HFC (hydrofluoro-carbon) solvents, followed by vapour rinsing and freeboard drying to facilitate precision component cleaning. Typical Microsolve applications include precision cleaning of bearings, gyro components, connectors and interconnects, maintenance cleaning of aerospace power generation system components and pneumatic and hydraulic components. And in electronics, flux removal from PCBs, including no-clean and lead-free solder flux residues, and from soldering jigs and fixtures.
Spray Washing
The Guyson Orbit - single-stage, rotary basket - spray washer is available in two standard sizes: the Orbit 800 is the most popular size while the compact Orbit 600 fits into a smaller footprint. These top loading spray washers offer excellent cleaning results, with a motor-driven rotating basket carrying the components under the highly effective spray jets. These machines are often used in manufacturing cells and regularly used for degreasing flap actuation gears. Aerospace MRO is another use of the Orbits cleaning power on projects such as cleaning landing gear and brakes. Additionally, they can be used for the removal of general dirt and grime from both aluminium and steel aeronautical ground lighting (AGL) castings during maintenance; allowing them to be handled safely whilst being disassembled.
For further information on the range of equipment Guyson are able to offer the Aerospace market to download our free Aerospace products brochure.